2022年6月28日上午,上海张江国家自主创新示范区专项发展资金重大项目——“上海长兴海洋智能装备创新平台(一期)建设”项目顺利通过项目结题验收。专家组认为上海交通大学课题组通过对基于5G的船舶小组立信息物理融合生产线、船舶小组立构件智能焊接平台技术、大型船舶巨型总段柔性自动对接系统、基于5G的船厂关键工艺智能质量控制体系等四项关键技术的研究,较为出色地构建了基于5G的智慧船厂车间应用示范平台,并获得了丰富的学术成果。这为进一步探索和建立一套完整的船厂智能制造平台体系提供了前进方向,对优化和规范船厂生产制造新形态有着深远的影响和意义。
本项目通过验收的设备样机将于今年下半年入驻上海长兴海洋实验室4号楼—智能制造实验室,成为助推上海长兴海洋实验室建设的重要力量。
关键技术点1:基于5G的船舶小组立信息物理融合生产线
船体零部件制造车间每天加工数万零件,形状不规则、尺寸大小不一,依靠人工搬运和装配,工作负荷大;作业区域广,切割、理料、分拣、搬运和装焊的协作程度较低,作业过程易出错、效率低,零件大量堆积,延长船体分段建造周期。本项目开发了模型驱动的船舶小组立信息物理融合生产线,实现船体零件的自动分拣、搬运、识别和装焊,自主研发了切割零件的金属二维码自动标刻装置、自动分拣装置和小组立零件的自动装焊装置,开发了基于5G的小组立生产过程智能协同管控系统,实现船舶小组立的自动化、智能化生产,从而大幅提高生产效率。
主要创新点如下:
(1)建立了设计的切割版图和船板切割实体零件之间的模型与零件几何空间映射关系,开发了切割版图驱动的船体零件二维码自动标刻装置,为后续不规则零件的自动识别奠定了基础。
(2)建立零件的几何形状、加工工艺、组立三维模型、实物零件和空间位置等数据的关联关系,设计了船体零件和搬运装置之间数据交互机制,开发了船体零件的自动分拣装置,实现零件依据工艺流向和所属组立的自动分拣。
(3)研究组立三维模型,切割版图和制造工艺的数据模型,开发基于金属二维码的不规则零件自动识别系统,建立视图零件、识别系统,自动装备和数据模型等组成的信息物理融合系统,研制基于信息物理融合的小组立自动装焊装置,实现零件的自动识别、搬运、定位和装焊。
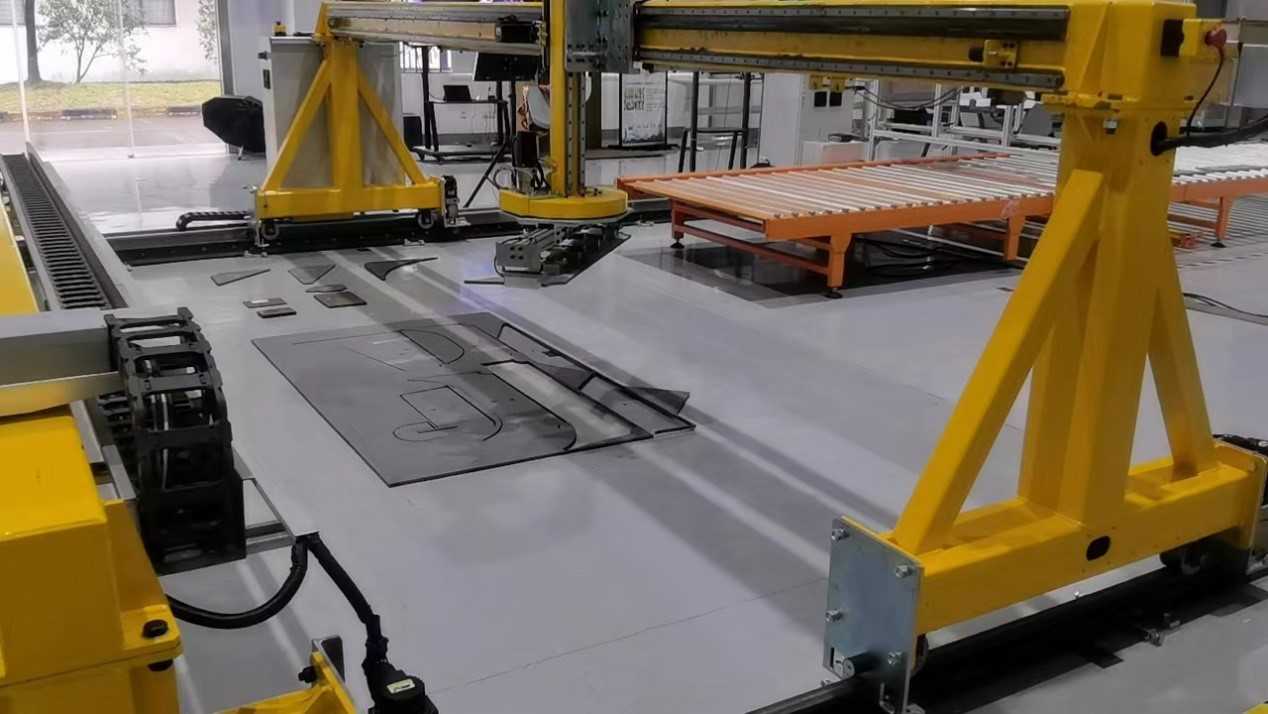
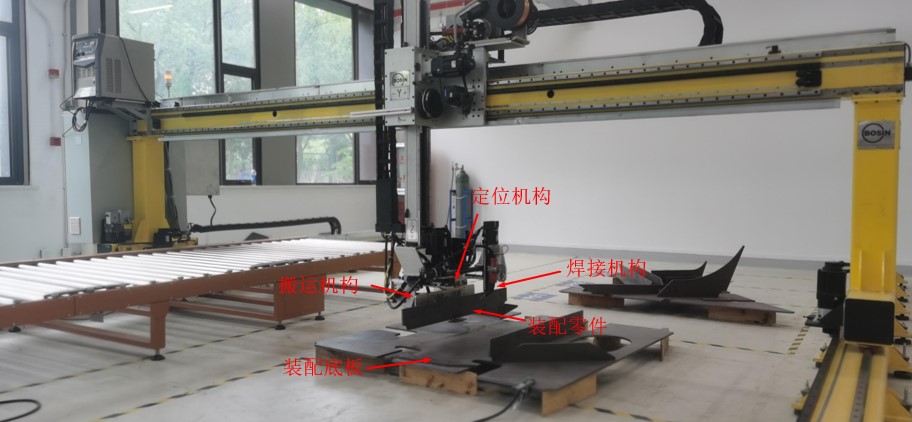
图1.小组立信息物理融合生产线
关键技术点2:船舶小组立构件智能焊接平台技术
船舶分段制造小组立部件焊缝以平角焊为主,结构具有一定的重复性,是船舶制造中适合采用机器人焊接系统的制造环节之一。而传统的示教再现式机器人焊接系统需要频繁进行人工示教,过程繁琐耗时长,已无法满足需求。本项目针对小组立部件开发了无示教自主规划机器人智能焊接系统,能够实现无固定工装,现场随意放置的大型结构件的自适应机器人焊接,并自主开发了系列核心工业软件,包括:焊缝自动提取软件、环境目标识别与定位软件、焊接机器人自主路径规划软件、自适应过程控制软件,为机器人智能焊接提供深度技术融合,实现机器人的手、眼、脑合一,极大提升多规格、小批量生产场景的焊接效率。
主要创新点如下:
(1)基于零件三维数模,建立了通用可识别的数字化文件标准,实现了零件的尺寸、焊缝信息及焊接工艺信息的统一识别与处理,建立了小组立构件双机机器人仿真模型。
(2)开发了多线激光3D视觉构件识别系统,统一了机器人-零件-3D视觉传感器坐标系,实现零件点云的提取,自动获得目标零件的实际位置信息,定位精度误差可达±5mm,1°以内。
(3)开发了粗定位条件下裕度自适应匹配的路径优化策略与避障算法,实现了机器人自主路径规划,规划算法结果与机器人轨迹运行结果完全吻合,避障成功率100%,匹配焊枪初始姿态实现焊缝寻位与跟踪,焊缝跟踪精度<0.5mm。
项目研究成果为船舶行业多板厚复杂工况及多尺寸小组立构件自动识别、自动定位等智能焊接技术提供了技术研发平台。解决了船舶行业小组立制造的共性关键技术,具有自主知识产权,达到了国内领先水平,项目的技术成果具有重大的推广意义及应用价值。
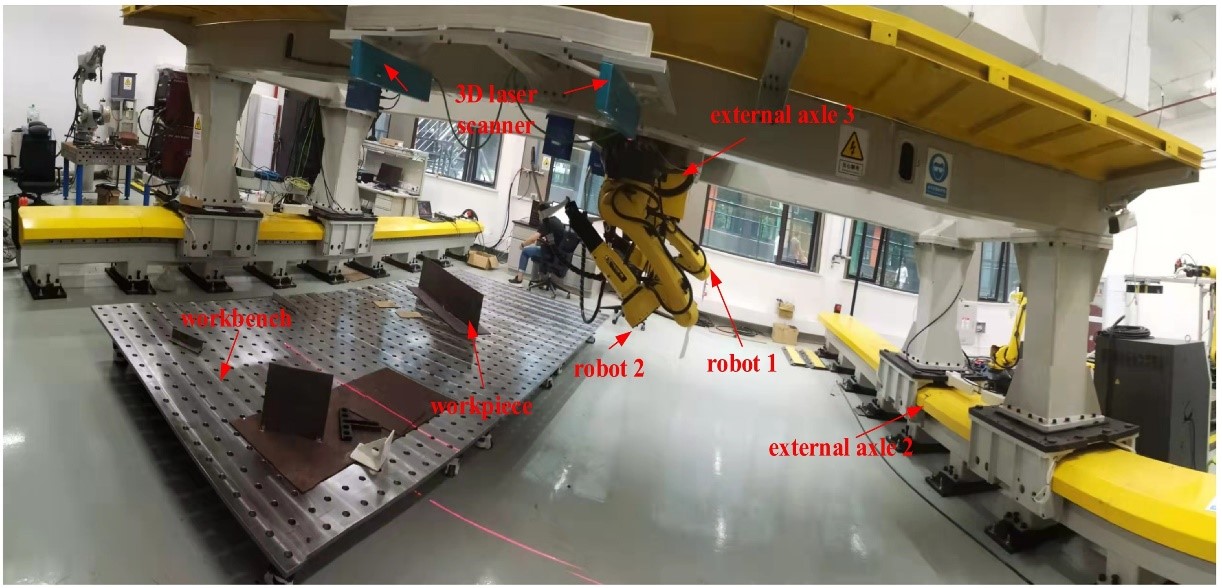
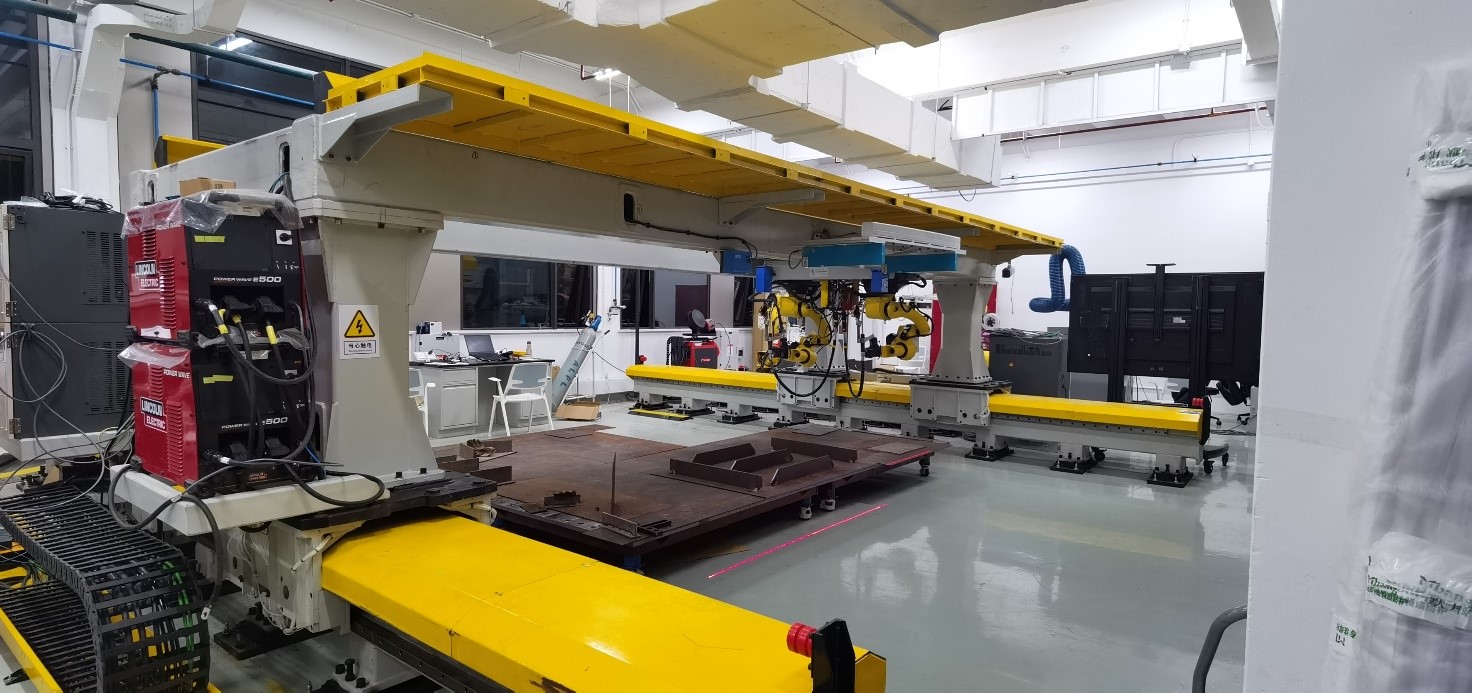
图2.小组立构件智能焊接平台
关键技术点3:大型船舶巨型总段柔性自动对接系统
巨型总段建造模式采用模块化分段制造,大大减少了对船坞、起重设备等船厂核心资源的依赖,是提高船舶行业制造质量和建造效率的有效途径。传统造船模式吊装起重设备调姿能力不足、运动控制复杂、定位精度较低,而且缺乏有效的测量设备来指导调姿定位,导致需要根据工人经验进行反复试凑,对接过程耗时费力,难以发挥总段建造模式的内在优势。本项目针对大型船舶巨型总段对接过程中,总段结构复杂、尺寸庞大、自重载荷高、对接精度要求高以及建造周期长等痛点,提出了采用群组定位机构协同调姿的柔性自动对接技术,开发了集“测量-匹配-调姿” 于一体的自动对接系统,解决了现有总段对接精度低、调整周期长、人工作业繁重、自动化程度低的难题,实现了大型船舶巨型总段的精确高效柔性对接,提高了船舶建造的效率。
主要创新点如下:
(1)实现了船舶巨型总段位姿高精度实时在位测量技术,测量误差<0.5mm,建立了巨型总段三维重建方法,实现关键对接特征的自动识别;
(2)设计制作了高精度巨型总段调姿定位机构,总承载能力大于4000吨,实现巨型总段结构变形的主动控制与总段位姿主动调整, 定位精度<0.5mm;
(3)建立了总段对接匹配评价指标,提出了最优位姿匹配算法,为总段对接提供理论支撑;
(4)研制开发了具有灵活运动能力的重载高精度调姿定位机构,优化了对接系统中调姿定位机构的群组布局,建立了冗余并联机构精度标定方法,完成了硬件驱动调姿算法,实现了冗余驱动的协同控制;
(5)开发了集“测量-匹配-调姿” 于一体的自动对接系统,开发对应的测量、计算、驱动软件和总控软件,系统最终可实现总段对接精度<2mm,对接调姿时间缩短50%以上。
项目研究成果为大型船舶巨型总段的对接合拢提供了柔性化、自动化的高质高效解决方案,为工业大场景实时在位高精度测量、调姿定位机构研制开发、冗余驱动群组协调控制、最优匹配算法设计等提供了技术研发平台。解决了船舶行业小组立制造的共性关键技术,具有自主知识产权,达到了国内领先水平,项目的技术成果具有重大的推广意义及应用价值。
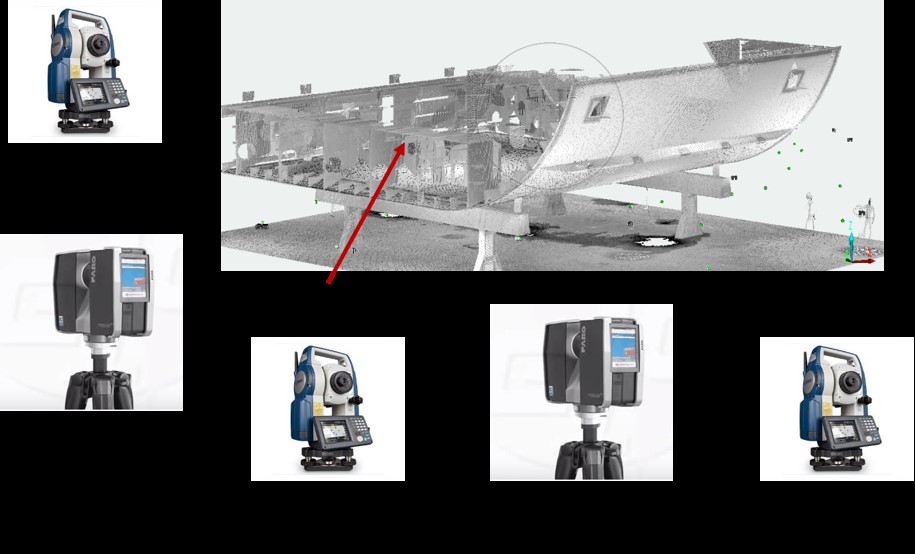
图3.总段位姿高精度实时在位测量
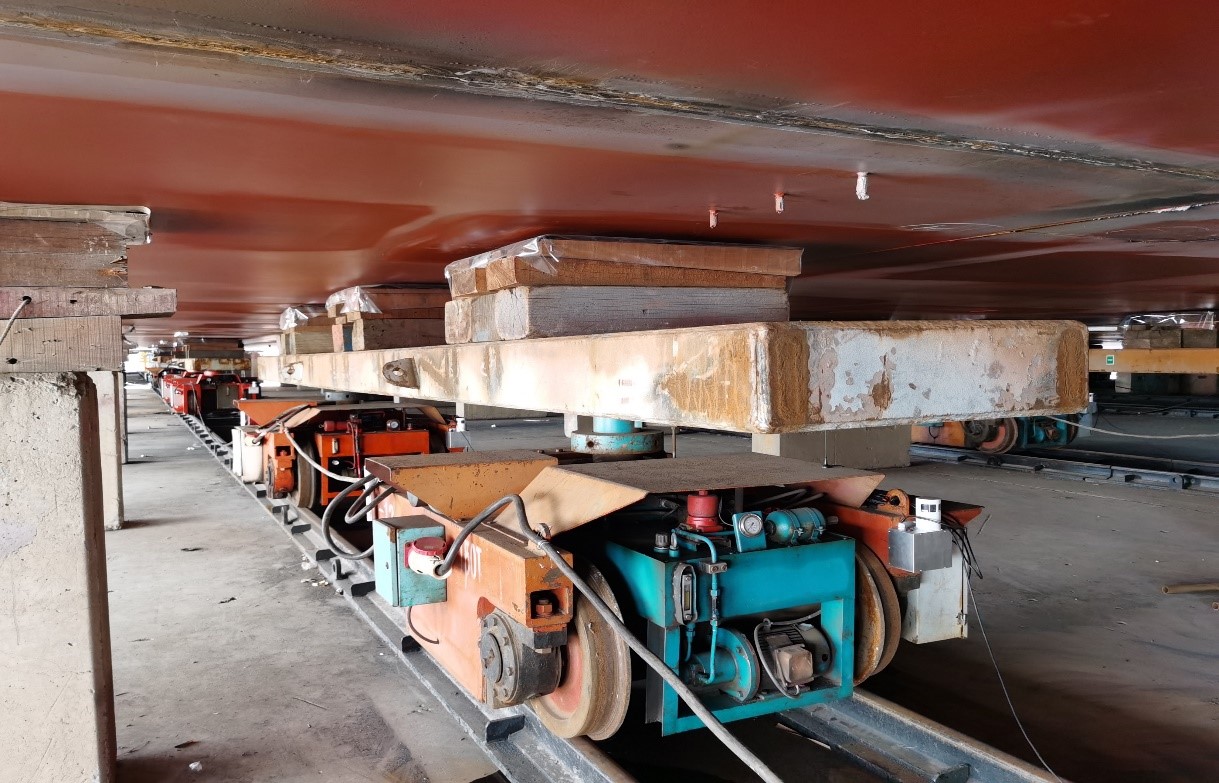
图4.调姿定位群组
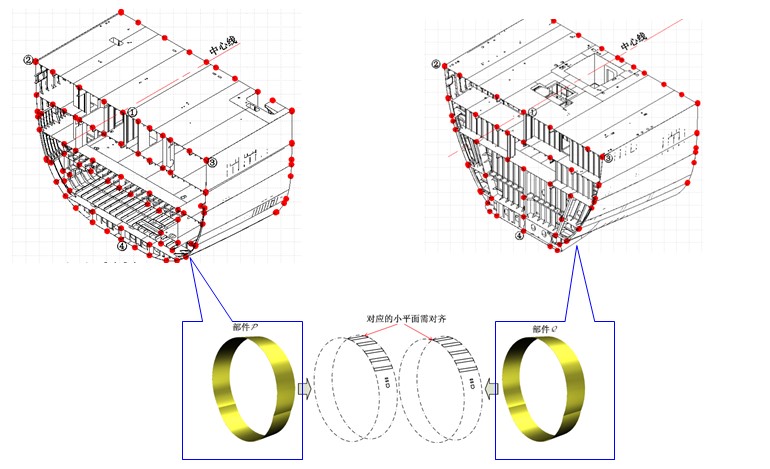
图5.最优位姿匹配评价算法
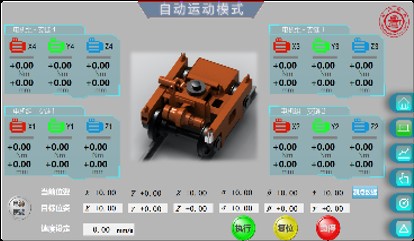
图6.调姿机构控制软件
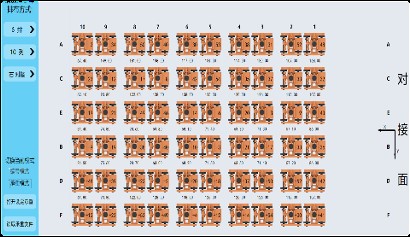
图7.冗余驱动协同控制算法
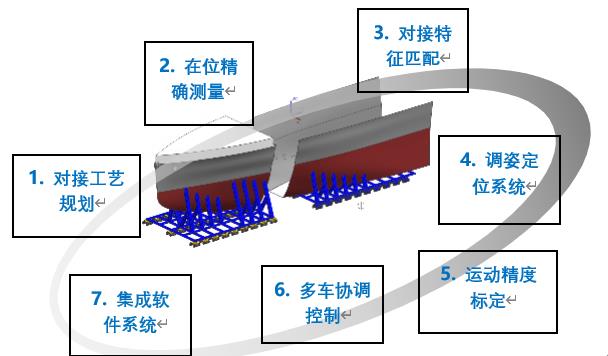
图8.“测量-匹配-调姿”自动对接系统
关键技术点4:基于5G的船厂关键工艺智能质量控制体系
(1)基于5G的船厂关键工艺智能质量控制体系
针对船体装配过程效率低、周期长、质量波动大等问题,分析船体建造的装配工艺流程,围绕主要装配部件的工艺特征,构建涵盖面向智能装配的曲面薄板拼接夹具布局优化技术、面向智能工艺控制的多工序偏差流建模诊断技术的研究框架。通过有限元方法与多目标优化算法的创新结合,优化了关键装配工序中夹具的布局方式;通过多工序偏差流建模方法,有效预测小组立装配过程中的偏差。最终,实现装配精度的提高、装配过程质量分析与预测能力的提升,将船体装配结构变形的质量控制技术从事后拓展到事前阶段,有效保证船体装配过程的质量与效率。
(2)面向智能装配的曲面薄板拼接夹具布局优化技术
在船体装配过程中,大型曲面薄板作为船体的基础板,对船体的装配质量起着关键作用。在实际生产中支柱式胎架等间距放置,以支撑曲面薄板(如图9所示),但由于重力等因素引起的零件形变,导致零件在装配边缘处间隙过大,焊接前需要进行人工调整以满足精度要求。
针对当前曲面薄板对接过程自动化水平低、人工矫正效率低、装配质量难以保证等问题,开发结合直接刚度法与多目标优化算法的夹具布局优化方法。该方法创新考虑了重力作用下大型曲面薄板变形带来的装配尺寸偏差,推导了考虑夹具约束的直接刚度法;并以关键质量指标为优化目标、以装配精度要求为约束,建立了0-1二进制整数规划模型;最后,采用多目标优化算法求解得到最优的夹具布局方案。
采用优化后的夹具布局方案(如图10所示),实现了对面薄板对接精度的有效控制,待拼接零件的装配边缘平均尺寸间隙减少90%以上,装配边缘处没有明显间隙(如图11所示),符合精度要求。
(3)面向智能工艺控制的多工序偏差流建模诊断技术
船舶建造过程的工序偏差传递机制,是分析与预测船舶装配过程质量、有效识别装配偏差源的诊断基础。但目前船舶制造过程偏差传递机制不明,无法准确判断偏差源,严重影响着船舶建造中的过程稳定性和质量一致性。
针对小组立装配过程中偏差传递机制不明、精度管控较弱等问题,结合有限元仿真技术,并运用状态空间方程对船底分段装焊过程中的偏差流进行建模。主要总结了船体分段精度质量偏差来源(如图12所示),并利用仿真软件建立的有限元模型得到板件对接装配变形预测结果(如图13所示),进而分析零件自身偏差、零件定位偏差和因对接变形产生的偏差在工序间累积和传递的过程。
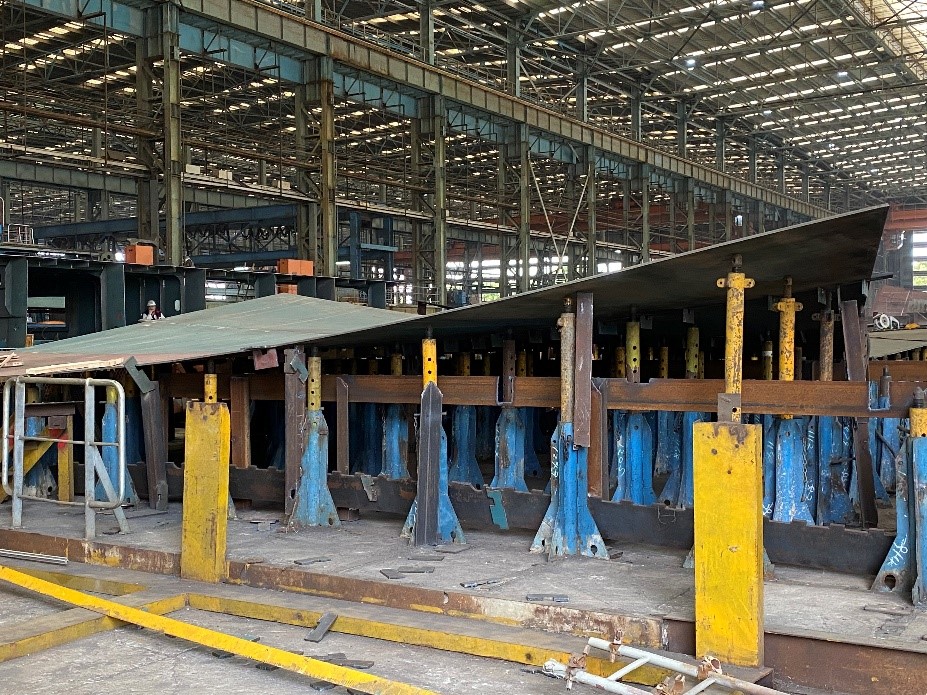
图9.曲面薄板放置于支柱式胎架上
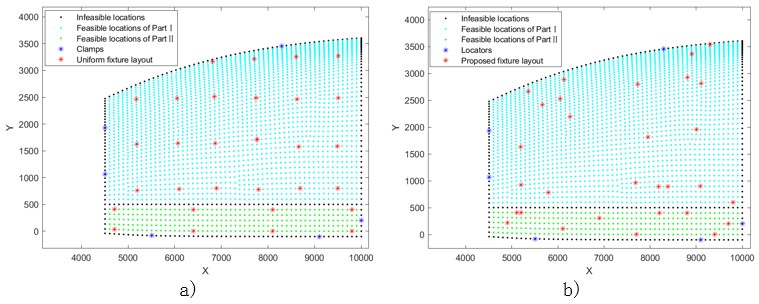
图10.夹具布局方式:a)现行夹具布局方式,b)优化后夹具布局方式
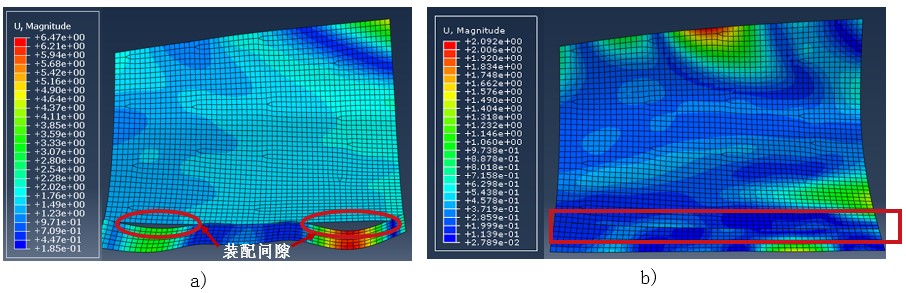
图11.零件变形情况:a)现行夹具布局下零件变形,b)优化后夹具布局下零件变形
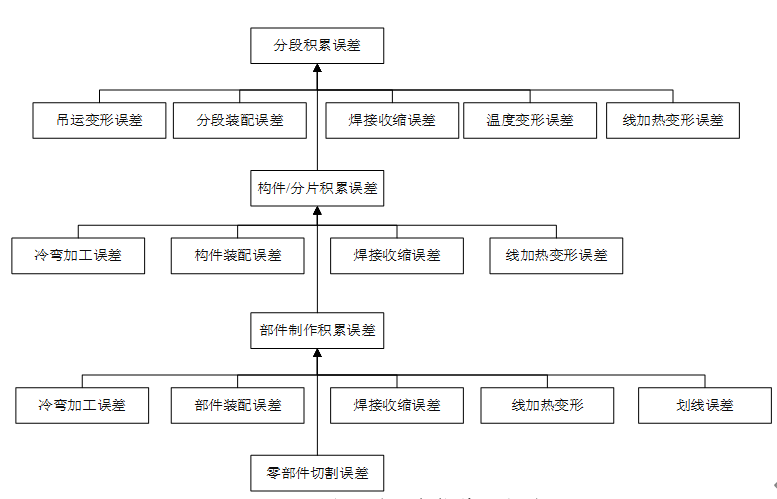
图12.分段建造过程中偏差累积过程
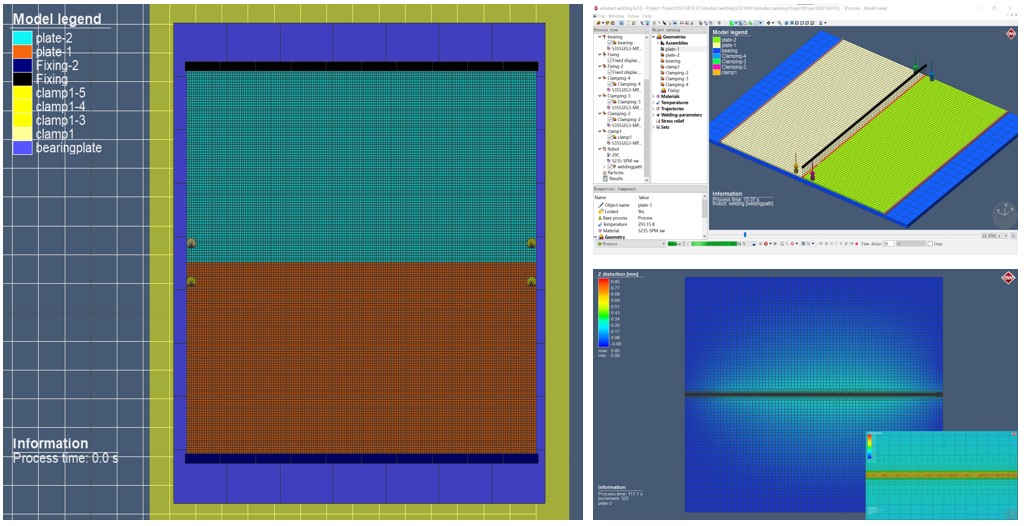
图13.板件对接装配有限元建模及仿真预测结果