技术背景
基于跨部门、多领域的统一数据建模和数字孪生驱动的无人化产线控制技术自主研发船舶小组立无人化产线,包括4套自动化装备和1套数据模型驱动的AI控制系统,是小组立智能制造新模式的探索,有助于大幅提升制造效率和准确率,还用机器人将工人从有危害、繁重的作业环境中解脱出来。
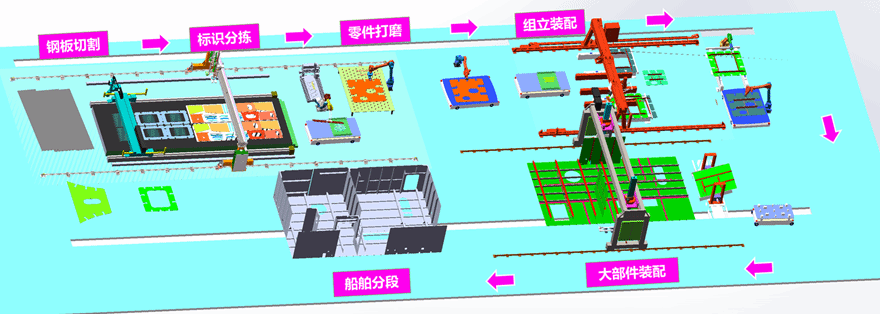
技术内容
1、自动化装备研制
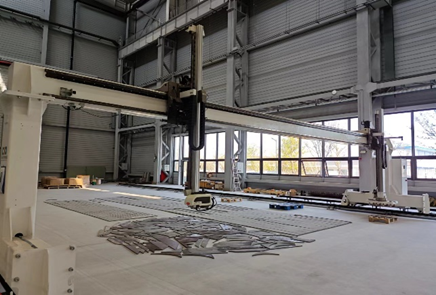
零件标识与分拣装备
依据切割版图,自动计算零件标识位置及抓取位置;依据组立BOM及零件流向,完成零件自动化标识与分拣。分拣设备平均运行速度700mm/s,平均分拣时间35S/个。
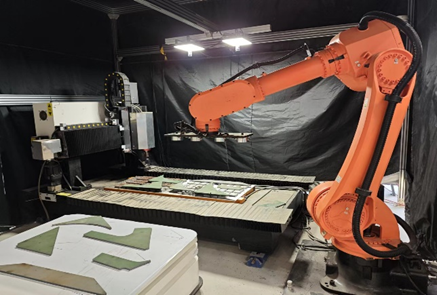
零件自由边打磨装备
依据零件模型获取自由边的几何信息,计算零件自由边打磨轨迹;匹配工艺知识库完成打磨参数选择,完成零件自由边的双边自动打磨,平均打磨速度2m/min。
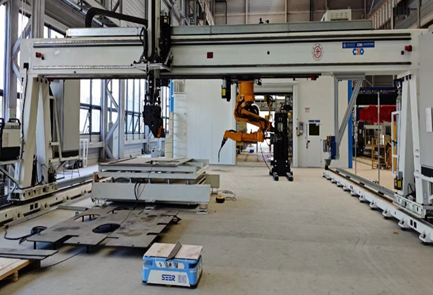
小组立智能装焊装备
依据小组立设计模型解析零件焊接边、焊接位置等信息;结合物理空间位置信息,规划装配抓取和点焊路径;基于焊接工艺知识库完成焊接参数设置,完成筋板的自动装焊,单个零件平均装焊时间3min。
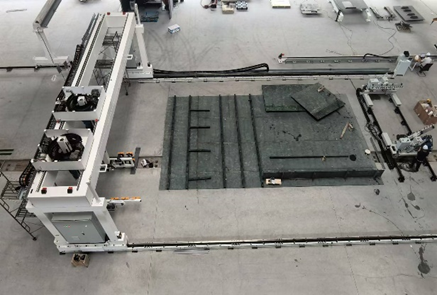
大部件智能装配装备
依据大部件设计模型获取纵壁、肋板、型材等的装配位置与BOM信息,依靠翻转装置与型材定位工装协同实现大尺寸、吨级舱壁的大部件自动装配,单个小组立平均装配时间2min。
2、智能管控软件开发
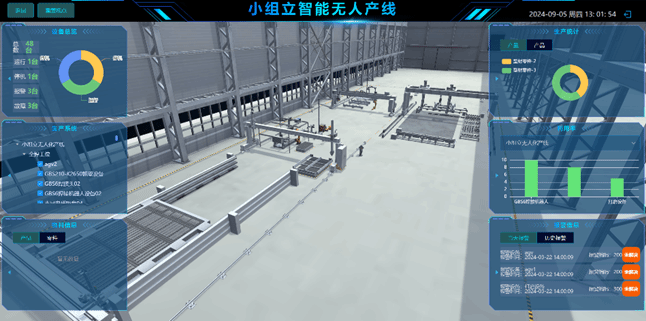
开发基于数字孪生的产线智能管控系统,基于物联网实时采集工位数据,支持实现数字域与物理域的实时同步,生产看板与指标、异常面板,产线动态计划预测与异常预警等功能。
应用场景
无人产线技术方案咨询
单台自动化装备的研制
小组立无人产线的研制
船舶建造软件系统开发
组立制造数据模型设计
组立无人制造流程测试
数字孪生制造技术培训
无人产线成果转移转化